La optimización logística para la gestión de almacenes se refiere a un conjunto de prácticas orientadas a mejorar la eficiencia en los procesos de almacenamiento y entrega.
El objetivo principal es garantizar el abastecimiento continuo y poder hacer frente al aumento de la demanda. En este artículo te explicaremos cuáles son los factores clave para hacer que un almacén sea eficiente y cómo puedes optimizar las operaciones logísticas más habituales.
¿Cuáles son los aspectos clave en la gestión de almacenes?
Para que los almacenes funcionen correctamente debemos tener en cuenta algunos aspectos básicos en su gestión.
- Espacio: buscamos siempre el aprovechamiento óptimo del espacio disponible con el fin de aumentar la capacidad de carga del almacén. Sin embargo, este aprovechamiento no debe implicar desorganización o una pérdida de accesibilidad a los productos.
- Stock: hay que determinar el stock mínimo necesario de cada producto para no almacenar cantidades innecesarias. Para lograrlo es esencial hacer una previsión precisa de la demanda.
- Coordinación: el almacén debe coordinarse con otros departamentos de la empresa (como el departamento de ventas) para determinar la cantidad de productos que entran y salen.
- Trazabilidad: consiste en hacer un seguimiento del movimiento de los productos, conocer su ubicación exacta, detectar desperfectos o pérdidas de inventario. La trazabilidad proporciona una base de datos completa que podemos utilizar para evaluar el rendimiento del almacén, tomar decisiones informadas y establecer objetivos comerciales.
¿Cómo hacer más eficiente la gestión de almacenes?
Una buena gestión implica, generalmente, implementar estrategias que mejoren la productividad, minimicen los costos asociados al almacenaje y distribución, reduzcan los tiempos de entrega y aumenten la satisfacción del cliente. Todo esto se reflejará en un mejor desempeño de la empresa en su conjunto.
Estas estrategias incluyen:
- La reorganización del almacén para maximizar su espacio y su uso.
- La utilización de tecnologías avanzadas para agilizar la gestión de inventario.
- La integración de robots y otros sistemas de almacenamiento automatizado.
- El uso de tecnologías de control de calidad para garantizar la fiabilidad de los productos.
- Mejoras en los procesos de embalaje para proteger la mercancía durante el transporte.
- Mejoras en los procesos de entrega para evitar retrasos. Por ejemplo, establecer puntos de recogida estándar.
- Uso de herramientas de planificación que coordinen la disponibilidad de los productos en toda la cadena de suministro.
- Formar a los empleados para que sigan procedimientos precisos de control de inventario.
Además, es importante gestionar bien la demanda de los clientes para evitar el exceso de inventario o la falta de existencias. Utilizar un software de análisis de datos es una buena forma de tomar decisiones informadas y racionalizar la compra de mercancías.
¿Cuáles son las operaciones logísticas habituales en la gestión de almacenes y cómo se pueden optimizar?
La gestión de almacenes implica la realización repetitiva de una serie de procedimientos logísticos que tienen como finalidad asegurarse de que el inventario se administra de manera eficiente y los procesos de almacenamiento y envío son fiables y seguros.
Recepción de mercancías
Es el momento en el que los productos se reciben en el almacén. Esta operación consiste en comprobar que la mercancía está completa y en buenas condiciones.
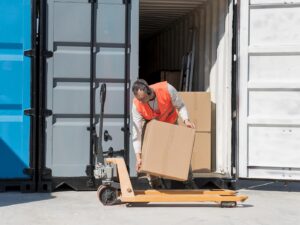
El proceso debe realizarse de manera ágil y eficiente para garantizar que los productos lleguen a tiempo al mercado. Para conseguirlo, los empleados deben tener un conocimiento completo de los requisitos de seguridad y los procedimientos de recepción. Además, deben estar provistos de los equipos adecuados: contenedores de almacenamiento, dispositivos de lectura de código de barras, etc.
Una buena estrategia para optimizar la recepción de mercancías es integrar la identificación automatizada (AIDC) en el proceso. Esto significa usar tecnologías como terminales móviles con lectores RFID integrados para controlar el contenido de los contenedores de manera rápida y sencilla. De esta manera el personal de almacén podrá obtener información exacta y actualizada sobre los productos en tiempo real, lo que mejora la eficiencia.
Almacenamiento
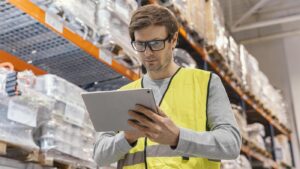
Consiste en identificar y clasificar la mercancía para su posterior recuperación. La idea es aprovechar al máximo el espacio disponible y asegurar un flujo de trabajo eficiente.
Para optimizar el almacenamiento debemos asignar a cada producto un lugar específico en el almacén que permita la creación de una “ruta de despacho óptima”. También sería importante seleccionar el equipamiento adecuado (contenedores, estantes, etiquetas de productos) e implementar un sistema de gestión de almacenes que haga un seguimiento preciso del movimiento de las mercancías dentro y fuera del almacén.
Picking
Es el proceso de preparación de un pedido en el almacén. Optimizar este procedimiento es de vital importancia para garantizar el buen funcionamiento de toda la cadena de suministro.
Actualmente, la preparación de pedidos representa el 60% de los costes operativos del almacén. Una mala ejecución de esta tarea podría ocasionar un cuello de botella y aumentar el tiempo que transcurre desde la recepción de la orden hasta la entrega final al cliente.
Las actividades que involucra el Picking son:
- Recepción del pedido
- Recorrido del almacén
- Selección de los productos
- Verificación del pedido
- Embalaje
- Envío
Hoy en día, casi todas las empresas utilizan algún software de automatización que interactúa con los trabajadores del almacén encargados del Picking. Los SGA (sistemas de gestión de almacenes) utilizan el análisis predictivo de datos para ayudar a las empresas a optimizar la gestión de almacenes.
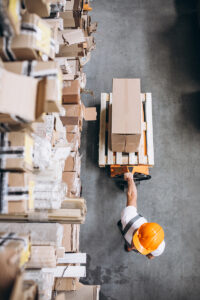
Ya en 2018 un informe de la consultora SoftDoit señaló que el 38,9% de las PYMES españolas que decidieron implementar esta solución tecnológica lograron aumentar su ROI en menos de un año. Los beneficios más importantes se traducen en un ahorro de los costes operativos y en una mejora de la satisfacción de los clientes y empleados.
Para alcanzar este incremento de la productividad, los SGA cuentan con una serie de herramientas y funciones que permiten, por ejemplo: hacer una previsión de la futura demanda, llevar el control de existencias, gestionar el flujo de pedidos, planificar el embalaje y el transporte, etc. Para que el sistema se integre con éxito es importante que disponga de una interfaz intuitiva y sencilla de utilizar y, al mismo tiempo, que sea escalable para responder a las necesidades de crecimiento de la empresa.
Por supuesto, los SGA no son la única solución tecnológica para optimizar el Picking. Existen otros métodos, por ejemplo:
- Radiofrecuencia (RF): es una tecnología de comunicación inalámbrica que utiliza un dispositivo para leer un código de barras o identificador RF. Estos dispositivos funcionan como asistentes digitales ofreciendo la ubicación exacta de los productos en el almacén sin tener que buscar manualmente en los estantes.
- Picking on light: se colocan unos pequeños leds en las estanterías donde se encuentran los productos para guiar a los operarios.
- Voice Picking: los empleados reciben las instrucciones para la recolección de los productos a través de comandos de voz inteligentes.
Packing
Es el proceso logístico que se encarga del embalaje y empaquetado del producto para ser enviado a su destino.
El Packing está muy relacionado con la satisfacción del cliente, por eso las empresas se esfuerzan en mejorar cualquier aspecto relacionado con la presentación del producto. Además, elegir los embalajes adecuados se refleja en una reducción de los costes logísticos del transporte al minimizar el peso y volumen de los pedidos. Es importante no desperdiciar espacio ni material, pero también proteger adecuadamente el artículo para evitar daños y desperfectos.
Una vez más, la utilización de los SGA es la mejor opción para un Packing exitoso. Estos programas determinarán cuál es el material de embalaje más adecuado según las características de cada producto.
Cuando el pedido esté correctamente empaquetado, los empleados del almacén lo entregarán a la empresa de transporte que introduce toda la información en el software para gestión de envíos. Por último, se imprimirá el albarán.
Cross docking
Es una práctica logística en la cual los productos se reciben directamente de los proveedores, se descargan y se redistribuyen al cliente final sin pasar por ningún almacenamiento a largo plazo.
Este método es frecuentemente utilizado por algunos vendedores minoristas para ahorrar los costes del mantenimiento de inventario y almacenamiento. Funciona especialmente bien con artículos de temporada que tienen una demanda muy limitada en el tiempo (por ejemplo, la decoración navideña).
Prescindir del almacén como eslabón intermedio entre proveedores y consumidores, exige una gran coordinación de todos los actores implicados.
Gestión de stocks
La finalidad de esta operación logística es llevar un control de las existencias para asegurar los niveles óptimos de inversión en inventario.
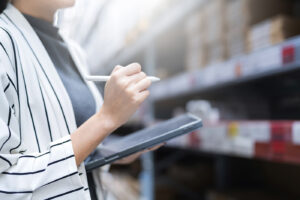
La forma más sencilla de hacerlo es utilizar un software de gestión que permita monitorear la cantidad exacta de mercancías que hay en el almacén. Así se evitan tanto las reposiciones excesivas como situaciones de bajo stock para satisfacer la demanda.
También es posible hacer una previsión de la demanda basada en datos históricos y patrones de comportamiento de los clientes. De esta manera, los administradores de los almacenes pueden prever con precisión los niveles óptimos de stock para cada producto y las cantidades apropiadas para reponer.
Distribución
Es la gestión de cualquier actividad relacionada con la entrega de productos al punto de venta final.
Dentro de este proceso tiene especial importancia la planificación de rutas, que se refiere a la creación de planes de entrega a partir de la información recopilada en el almacén. Esto implica el uso de datos sobre destinos, pedidos, horarios y otros detalles para programar los itinerarios y determinar cuáles son los mejores transportes disponibles.
Un software en la nube como MyMov puede ser la solución ideal para optimizar las rutas de reparto coordinando a los equipos del almacén con la empresa encargada del transporte de mercancías. No sólo evitarás incidencias y contratiempos, también reducirás los altos costes asociados a la logística de última milla (posiblemente los más elevados del proceso de venta).
La transformación digital es una tarea obligatoria para cualquier empresa (grande o pequeña) que se dedique a las operaciones logísticas. No te despistes y sigue estos consejos para adaptar tu negocio a los cambios frenéticos del mercado y seguir siendo competitivo.